Textile Boiler: Critical Applications and Strategic Importance
The textile industry’s reliance on textile boilers is deeply intertwined with its production workflows. Steam generated by boilers is essential for processes like fabric scouring, where impurities are removed using high-temperature steam; dyeing, which requires precise temperature control to ensure uniform color absorption; and printing, where steam activates dyes or chemicals to create intricate patterns. Additionally, steam is used in finishing processes such as calendering and heat setting, which enhance fabric texture and durability. Beyond direct production tasks, textile boilers must also maintain stable ambient temperatures in manufacturing environments to prevent material deformation or inconsistencies in moisture content.
Despite their indispensability, textile boilers confront several challenges. Energy efficiency remains a top priority, as steam generation often accounts for a significant portion of operational costs. Environmental compliance adds another layer of complexity, particularly in regions with strict emissions standards. Textile producers must also address the risk of steam quality fluctuations, which can lead to uneven dyeing, fabric defects, or machinery inefficiencies. Furthermore, the variability of fuel sources—whether natural gas, coal, or biomass—requires boilers to adapt to diverse input materials without compromising performance.
ZOZEN Boilers: Tailored Solutions for the Textile Sector
Among ZOZEN Boiler’s offerings, the SZL series of coal-fired steam boilers stands out as a robust and adaptable solution for textile manufacturers seeking a balance between cost-effectiveness and operational excellence. Designed with advanced combustion technology and a focus on steam stability, the SZL series addresses the core challenges faced by textile producers while ensuring compliance with environmental and efficiency benchmarks.
The SZL series coal-fired boiler is a chain grate water pipe boiler designed by ZOZEN Boiler based on international advanced technology and experience. It adopts a horizontal double drum and longitudinal layout structure. The boiler consists of two large parts, the upper large part is the main heating surface, and the lower large part is the combustion equipment. Water-cooled walls are arranged around the front of the boiler body to form a combustion chamber to absorb the radiant heat of the furnace; the convection tube bundle is arranged between the upper and lower drums at the rear end. After the fuel is burned in the furnace, the high-temperature flue gas is horizontally flushed on the heating surface of the convection tube bundle through the secondary return, and then led to the separately arranged economizer, and finally enters the dust collector.
The design of the chain grate and the independent wind bin ensures that the fuel is fully burned. The furnace adopts a densely arranged water-cooled wall tube structure, matched with a customized boiler system, with a large radiation area, so that the thermal efficiency is >81%. In addition, the SZL boiler has a wide adaptability to fuel, and can be used for a variety of coal types such as bituminous coal, lean coal, and anthracite.
In addition to the SZL coal-fired boiler, the ZOZEN WNS gas-fired steam boiler and the DZL biomass steam boiler are also good choices for the textile industry.
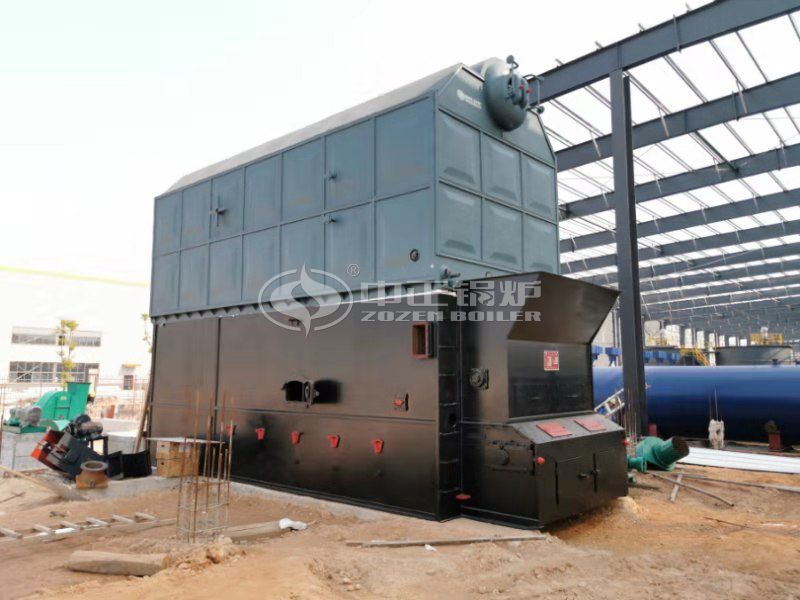
ZOZEN’s SZL Boiler Empowers Textile Production in Tajikistan
A compelling example of ZOZEN’s expertise in the textile sector is its collaboration with a leading textile manufacturer in Tajikistan. The client, a vertically integrated textile plant specializing in cotton processing, sought a reliable steam generation solution to support its dyeing, printing, and finishing operations. After an extensive evaluation of available options, the company selected ZOZEN’s SZL series 10-ton coal-fired steam boiler, recognizing its alignment with their operational and environmental objectives.
In this application, the SZL boiler was deployed to supply high-quality steam for multiple processes. During dyeing, the boiler’s stable steam output ensured even pigment absorption, reducing rework and material waste. In printing operations, precise temperature control enabled sharp, durable patterns, enhancing product aesthetics. The boiler’s ability to maintain a consistent thermal environment also proved vital for finishing processes like fabric stretching and heat setting, which require uniform conditions to achieve desired textures and durability.
ZOZEN’s technical team worked closely with the client to optimize the boiler’s integration into the plant’s existing infrastructure. The SZL series’ advanced water wall technology played a pivotal role in eliminating steam quality issues previously encountered with the client’s aging boiler system. By preventing excessive moisture or dryness in the steam, the new boiler minimized production disruptions and improved overall fabric quality. The client’s procurement process was facilitated by ZOZEN’s proactive market engagement, with the company leveraging its online presence and industry reputation to connect with the Tajikistan-based textile producer.
Comprehensive Support: ZOZEN’s Commitment to Customer Success
Beyond delivering high-performance boiler systems, ZOZEN Boilers distinguishes itself through its unwavering focus on customer support and after-sales service. Recognizing that the success of a textile boiler extends beyond installation, ZOZEN provides end-to-end assistance, from initial consultation to long-term maintenance. This approach ensures that clients receive tailored solutions that evolve with their changing needs, whether through fuel optimization strategies or upgrades to meet emerging regulatory requirements.
ZOZEN’s service network spans multiple regions, enabling rapid response to client inquiries and minimizing downtime in the event of technical issues. The company’s engineers are trained to address the complexities of textile boiler operations, offering on-site troubleshooting, remote diagnostics, and operator training programs. Additionally, ZOZEN’s preventive maintenance protocols leverage real-time monitoring systems to identify potential issues before they escalate, safeguarding the reliability of textile production lines.
For textile manufacturers, ZOZEN’s commitment to innovation and service excellence translates into measurable benefits. By reducing energy consumption, lowering emissions, and enhancing process consistency, ZOZEN’s boiler systems empower textile producers to achieve both economic and environmental goals. This holistic approach—combining cutting-edge technology with personalized support—has solidified ZOZEN’s reputation as a trusted partner in the textile industry’s journey toward sustainable growth.
In an era where industrial operations are increasingly scrutinized for their environmental impact and efficiency, ZOZEN’s approach to textile boiler design and service sets a new standard. Through continuous innovation and a deep understanding of industry-specific needs, ZOZEN ensures that every textile boiler it delivers becomes a cornerstone of its client’s success. For textile manufacturers worldwide, the choice of a boiler is not merely a technical decision—it is a strategic investment in the future of their craft.
LEAVE A MESSAGE
For all inquiries, please fill in the form below (* are required) to send us a brief message, and we will get back to you as soon as possible.